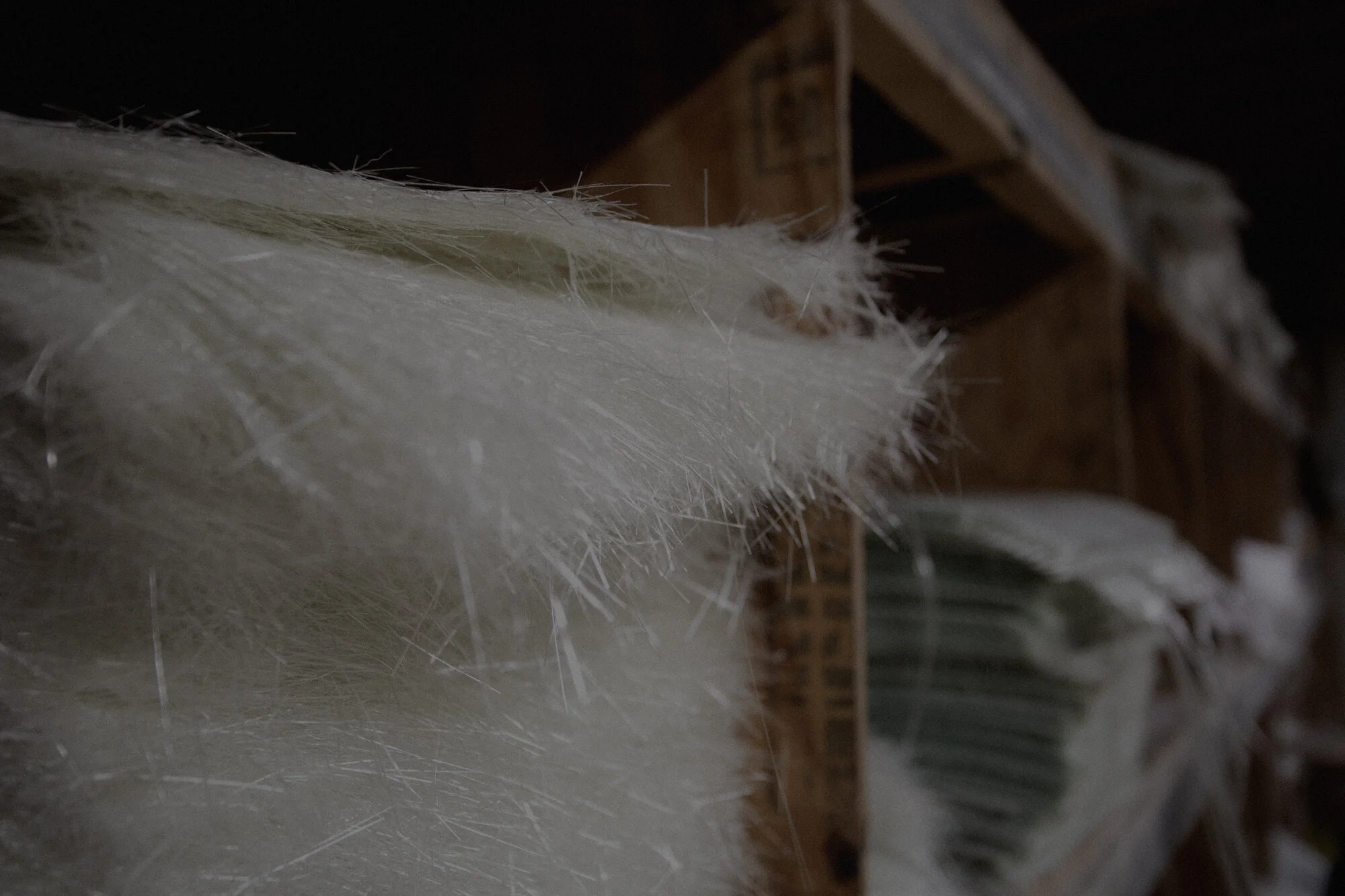
FRP Tank Manufacturing That’s Built to Last
Leverage our legacy of accuracy, quality and consistency
Not out to be the best-known. Just the best.
You value what’s built to last. At Allen Industries, we do, too. That’s why we hone in quickly on your unique tank storage needs — for starters, the task you need to undertake… the temperature, pressure and corrosiveness of your stored product… and the space or footprint you’re planning around.
If fiber-reinforced plastic storage containers (FRP) aren't an ideal option — and you’d be better off pursuing a stainless steel, mild steel, or plastic alternative — we’ll tell you right up front. And if FRP is a good fit, we’ll help you pinpoint and analyze the attributes vital to long-term performance and reliability.
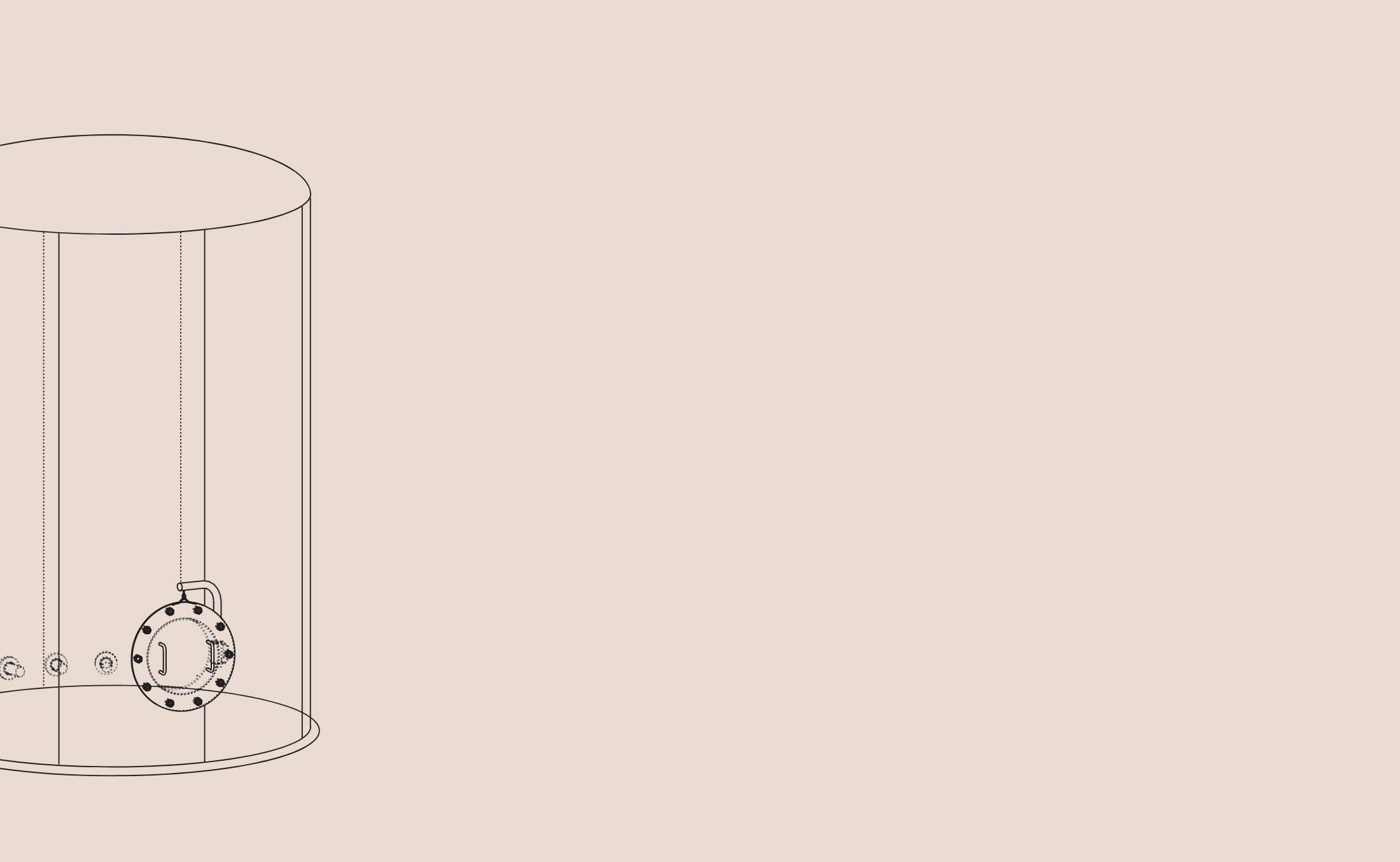
Balancing all the right variables
With thoroughly researched specs in hand, we can align your needs with the FRP tank platform that best readies you for success. Then we’ll craft a custom tank that gives you the assurance that’s only possible from a genuine build-to-suit solution that balances key variables, including:
Width impacts everything (including affordability, durability, and safety), especially with caustic chemicals.
Promoting the proper resin cure requires the proper catalyst, either MEKP or BPO/DMA. (And we can help you pick the right one for your application.)
Isophthalic or vinyl ester resin? Selecting the right option — the one with precisely the right mix of compatibility, strength, and other characteristics — is crucial to tank health.
By saturating a C-Veil or Nexus® membrane into your tank’s resin, you can count on the right veil to enhance performance and corrosion resistance.
Trusted to keep business flowing
Whether they’re spec’ing a 50-gallon surge tank or a 65,000-gallon water tank, engineers, contractors and facility managers in a broad range of industries have come to rely on us for unbiased advice, premier products, and best-in-class service when it comes to FRP tank manufacturing. That’s why Allen Industries FRP tanks are deployed so successfully in so many different applications across the U.S.
✕ TECHNOLOGY
Data centers, cooling water
✕ WATER TREATMENT
Sodium hypochlorite, ferric chloride
✕ GREEN ENERGY
Sodium hypochlorite, ferric chloride
✕ CHEMICALS
Bulk storage sodium, hypochlorite, hydrochloric acid, sulfuric acid and more
✕ AQUATIC DISPLAYS
Clean and balanced water sources
✕ FOOD & FEED INDUSTRY
Water, acids and FDA-approved feed oils
Put us to the test
You can rest assured that fit-for-purpose FRP tanks from Allen Industries will perform precisely to spec — and then some. Simple truth is, we won’t attach our nameplate to any tank that doesn’t represent our very best.
So as you weigh the pros and cons of various potential FRP tank manufacturers, we’d encourage you to evaluate all of them — us included — on these critical dynamics:
Cost
If a bid seems too good to be true, is there a clear reason why?
Transparency
Does your potential partner keep you in the loop and provide insights beyond the RFP?
Thoroughness
Regardless of how the specs are presented to the potential partner, are you asked for compliance requirements and questions about liner thicknesses, potential catalysts and resins, etc.?
Reputation
Are you about to say “Go!” to a company that’s recognized not just for producing a quality product, but also for excelling at after-sale service?

Excelling at process excellence
At Allen Industries, our Six-Sigma Lean Manufacturing-trained staff eagerly accepts that quality is the responsibility of our entire team. It’s our culture that ensures that QA processes are built into how we design, engineer, manufacture, and deliver every fiber-reinforced plastic storage container. So as our team grows, we continue to strictly adhere to quality standard guidelines that are specific to FRP manufacturing, including:
ASTM D2563
Classifying Visual Defects in Glass Reinforced Plastic Laminate PartsASTM D2583
Indentation Hardness of Plastic by Means of a Barcol ImpressorASTM D3299
Filament Wound Glass Fiber Reinforced Polyester Chemical Resistant TanksASTM D4097
Contact Molded Glass Fiber Reinforced Thermoset Resin Chemical Resistant Tanks
ASTM D2584
Standard Test Method for Ignition Loss of Cured Reinforced ResinsASTM C582
Contact Molded Reinforced Thermosetting Plastic (RTP) Laminates for Corrosion Resistant EquipmentASME RTP-1
An alternative standard that can be used for design and engineering calculationsANSI B16.5
For flanges (drilled to 150#)
